Construction IT Year-end Wrap & Look Ahead to 2023
LOOKING AHEAD INTO 2023
Process Orientation
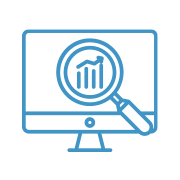
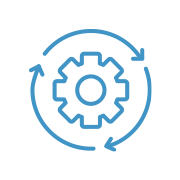
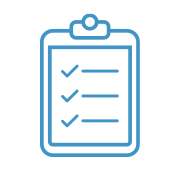
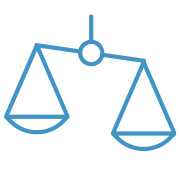
The Best Practice Assessment Tool
Allows you to gauge where your organization stands against industry average and best-in-class contractors.
Recalibrating IT
With the movement to Cloud infrastructure and solutions (SaaS) over the last ten years or so, traditional IT departments are faced with a need to change structure, makeup, and focus. The common emphasis on infrastructure is no longer as relevant as it once was. Contractor IT remains understaffed and underfunded for the job ahead, but IT also requires some rethinking in terms of the type of staff and use of outsourced resources and leveraging shadow IT.
For larger contractors, Burger Consulting Group has observed greater emphasis on IT Governance, the process of controlling IT spend, application selection and rollout, and managing enterprise applications. IT is no longer leading business transformation but instead assisting it through valuable support services, as they should be. Many contractors are also upgrading their lead IT person to function more as a Chief Information Officer (CIO) or IT Director and less as manager of infrastructure or applications.
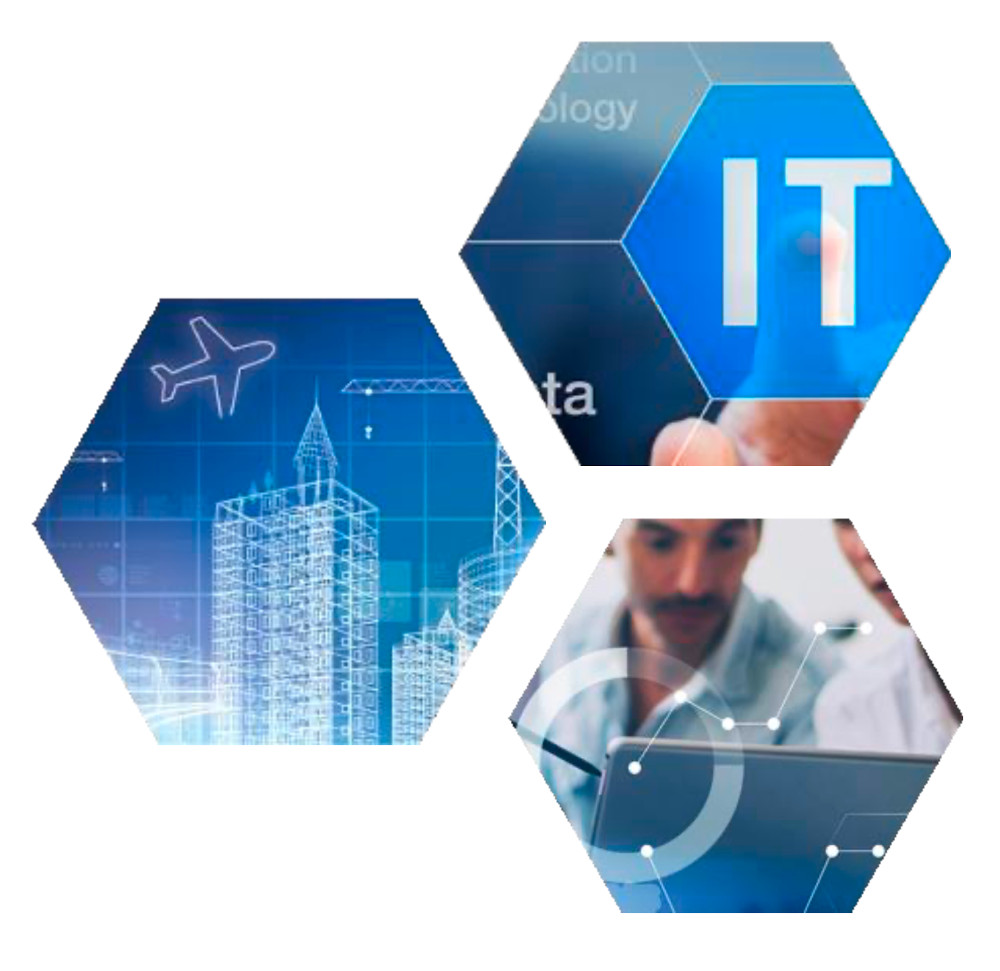
Human Resource and Payroll
The shortage of labor which has been an issue since we came out of the last downturn is having a dramatic effect on contractor strategy. Almost all contractors are focused on recruiting and developing their “human capital” as it is sometimes called. Contracting companies are now deploying larger Human Resource (HR) applications that include recruiting, onboarding, self-service portals, training administration, and sometimes even payroll. For Burger Consulting Group, the jury remains out on the viability of third-party payroll.
Some applications are evolving to oversee construction payroll while others are getting implemented to support specific payroll functions still done within the Enterprise Resource Planning (ERP) (e.g. certified payroll reporting). This is another good example of a process area which should be evaluated holistically, from recruiting through timesheets, payment, and benefits administration. When payroll is separated from the HR application, it will require a robust integration but that today seems easier than making do with an inadequate payroll solution that requires offline calculations or a lot of clumsy data movement. Timecard solutions are being divided as well, from those that are offered as bolt-on solutions from estimating solutions to stand-alone solutions that offer biometrics, time, date and Global Positioning System (GPS) stamping, and signature capture.
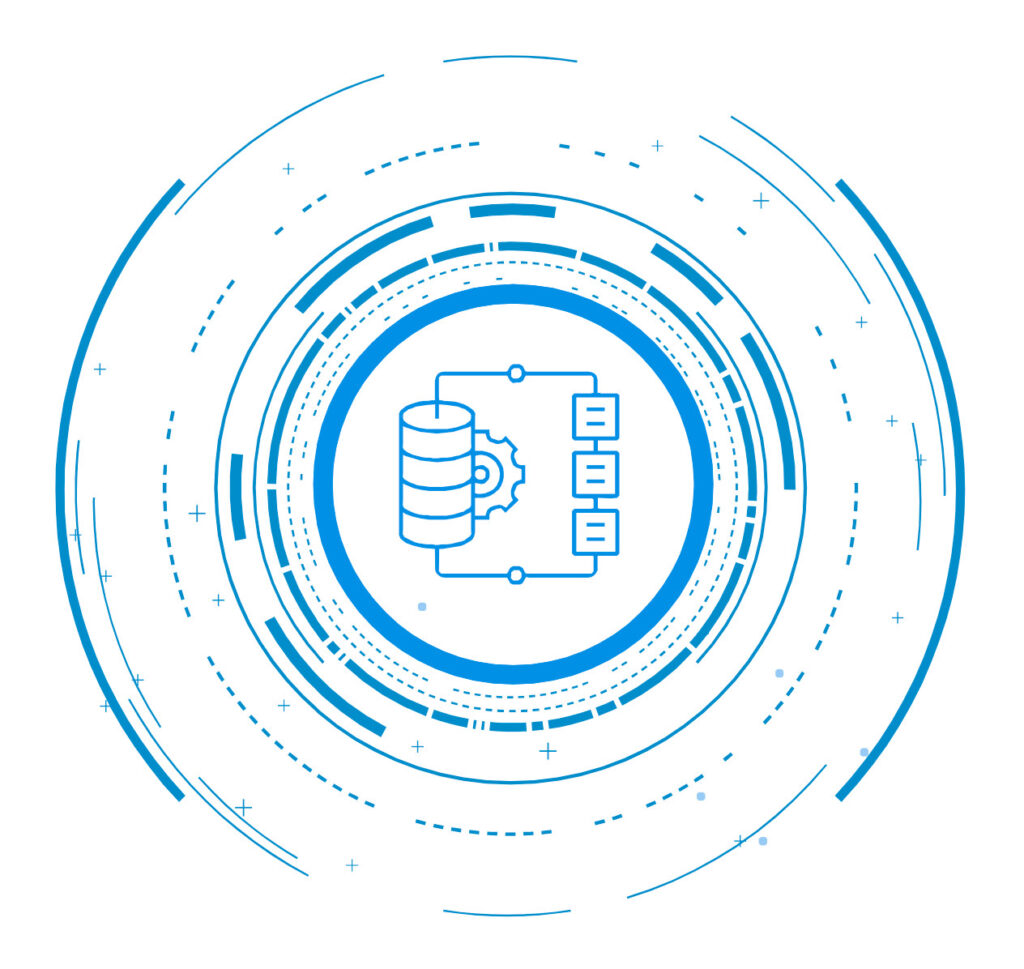
Integration
Data and Analytics
ERP
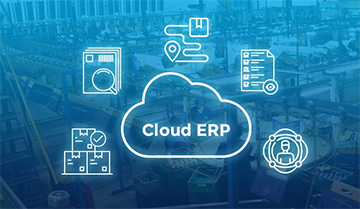
Industry Acquisition and Investment
While not a solution trend per se, changing capital structure of construction is already having an impact and will likely continue. Capital has been flooding into the industry from publicly traded companies and private sources. There has been an unprecedented level of acquisition and startup funding from incubators, private equity firms, and even contractors with their own funding sources.
The feeling is, given the state of the industry (i.e. behind in automation, largely inefficient), there is tremendous opportunity to capitalize on this large fragmented and antiquated space we call home. This will ultimately create a marketplace with more competition, more point solutions, and some degree of risk (not all well-conceived new solutions will survive). Our traditional business partners will change as well, becoming more profit centered and costly. And services are not a priority for many of these new developers. They are more focused on product development, not deployment and will leave the implementations to the customers or third-party providers. Trimble, Oracle, Thoma Brava, and Autodesk are good examples of the larger publicly traded firms that are purchasing firms and products at a robust rate and trying to create more value than the sum of their newly acquired products.
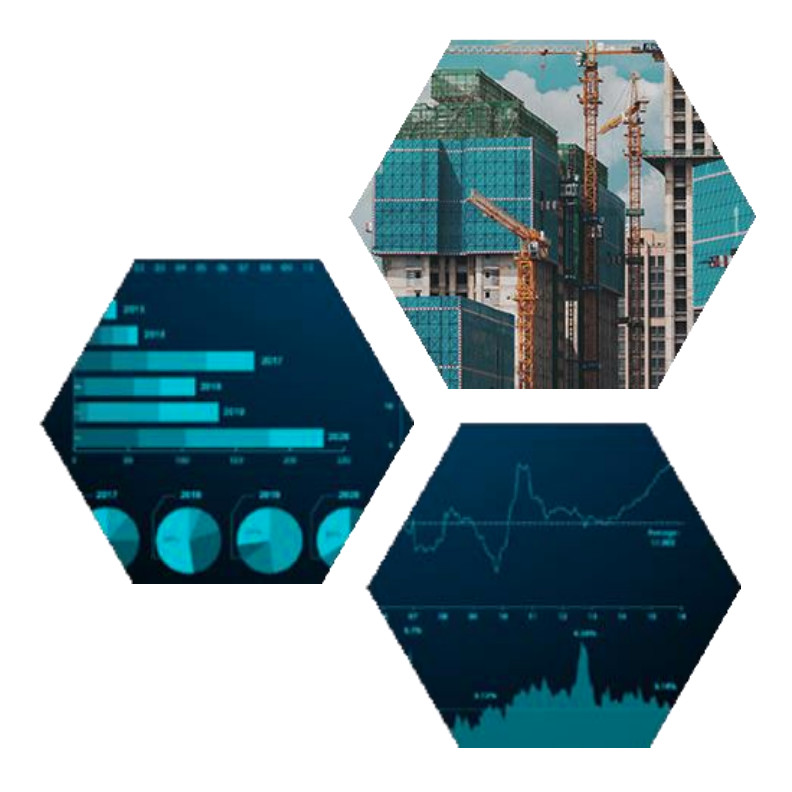
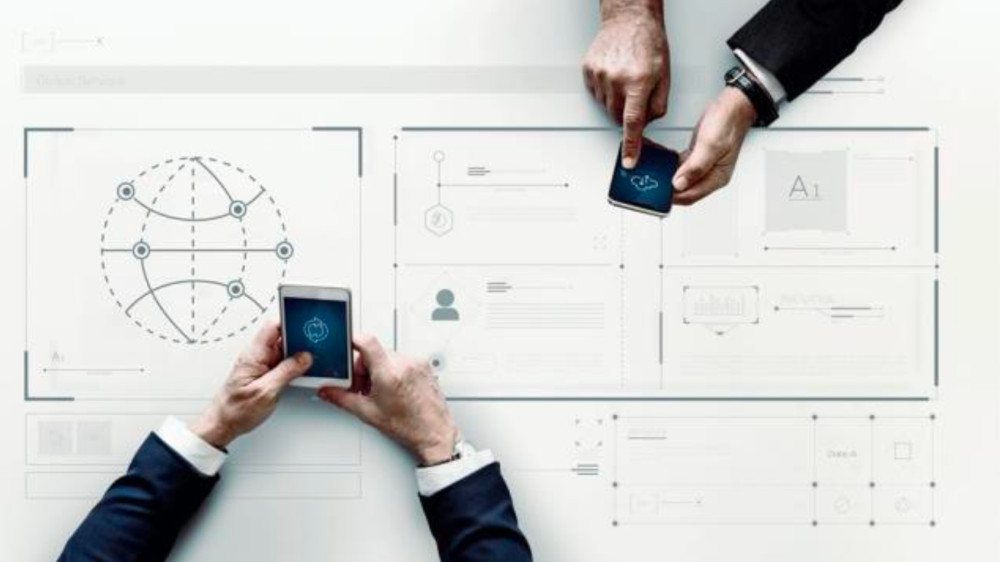
Estimating and Bidding
Equipment and Trucking
Heavy Civil Contractors, those that produce aggregate materials and simply those that have large fleets of heavy equipment are busy automating the management of their equipment as well as trucking and fuel management. Telematic devices have been available for a number of years now, but most contractors did not have much in the way of solutions to manage that incoming data.
In the past the movement of equipment, fueling, tracking of trucking, and preventive maintenance scheduling was handled on spreadsheets, magnet boards, and pieces of paper.
Today, thankfully, we have much more automated and efficient solutions to process this data and provide visibility into equipment utilization, fuel tracking, and delivery of materials to jobs.
This includes the downstream processing of material billing, job charging and inventory control. Burger Consulting Group has evaluated both Tenna and Clue for equipment telematics and preventive maintenance management as well as integration back to the ERP. The adoption of fuel management systems is on the rise as well with the advent of solutions like FuelCloud, Gasboy and Samsara. This is a complex area and definitely benefits from an end-to-end or at least integrated strategy.
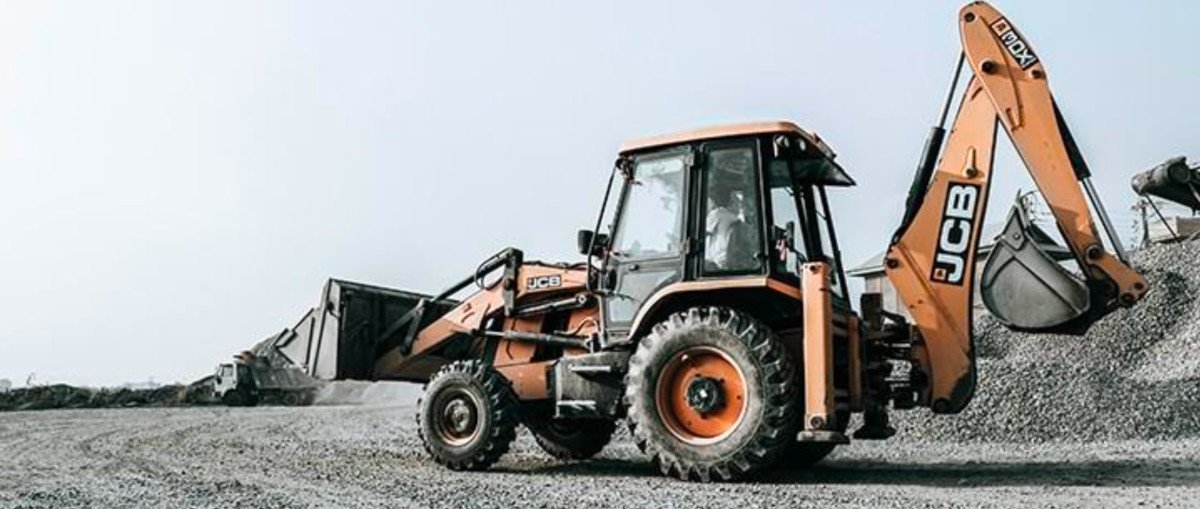
Prefabrication
Many specialty contractors, particularly those in MEP and drywall are moving quickly to develop their prefabrication capabilities. This is being driven by owners who see the value of prefabrication as well as the contactors themselves that grasp the efficiency inherent in fabricating in a controlled environment. This is impacting building information modeling (BIM), procurement, inventory control, and costing functions.
Most of today’s popular ERP solutions do not have all the necessary applications built in to manage a shopfloor’s operation. This will drive contractors to either evaluate ERP solutions that do (e.g. Acumatica, IFS, Dynamics) or find bolt-on solutions specifically made to control shop work orders, production control, logistics, and inventory management. Even General Contractors are feeling the need to develop some of their own prefabrication capabilities by doing panelization, prebuilt modular bathrooms or dorm rooms for example. This will require a greater leverage of Design for Manufacturing (DFMA) capabilities within their Virtual Design and Construction (VDC) departments.